Azoth's additive (3D) manufacturing technology is gaining widespread popularity and acceptance within the medical device manufacturing sector.
Our team of engineers at Azoth possess extensive expertise in medical components and upholds the most rigorous industry quality standards. We collaborate with you throughout the entire production process to guarantee the delivery of the highest quality parts within the shortest possible timeframe.
Unique Capabilities for Medical Manufacturing
Parts made with surgical precision – Azoth employs cutting edge additive manufacturing technology to produce tight tolerance components that meet the stringent demands of the medical industry.
Where other additive manufacturing technologies fall short, Azoth delivers a superior surface finish that is market ready with minimal post processing. From limited part runs to high-volume production, Azoth's technology seamlessly scales to meet varying demands, utilizing consistent equipment and processes. This eliminates the necessity for requalification, streamlining the manufacturing process.
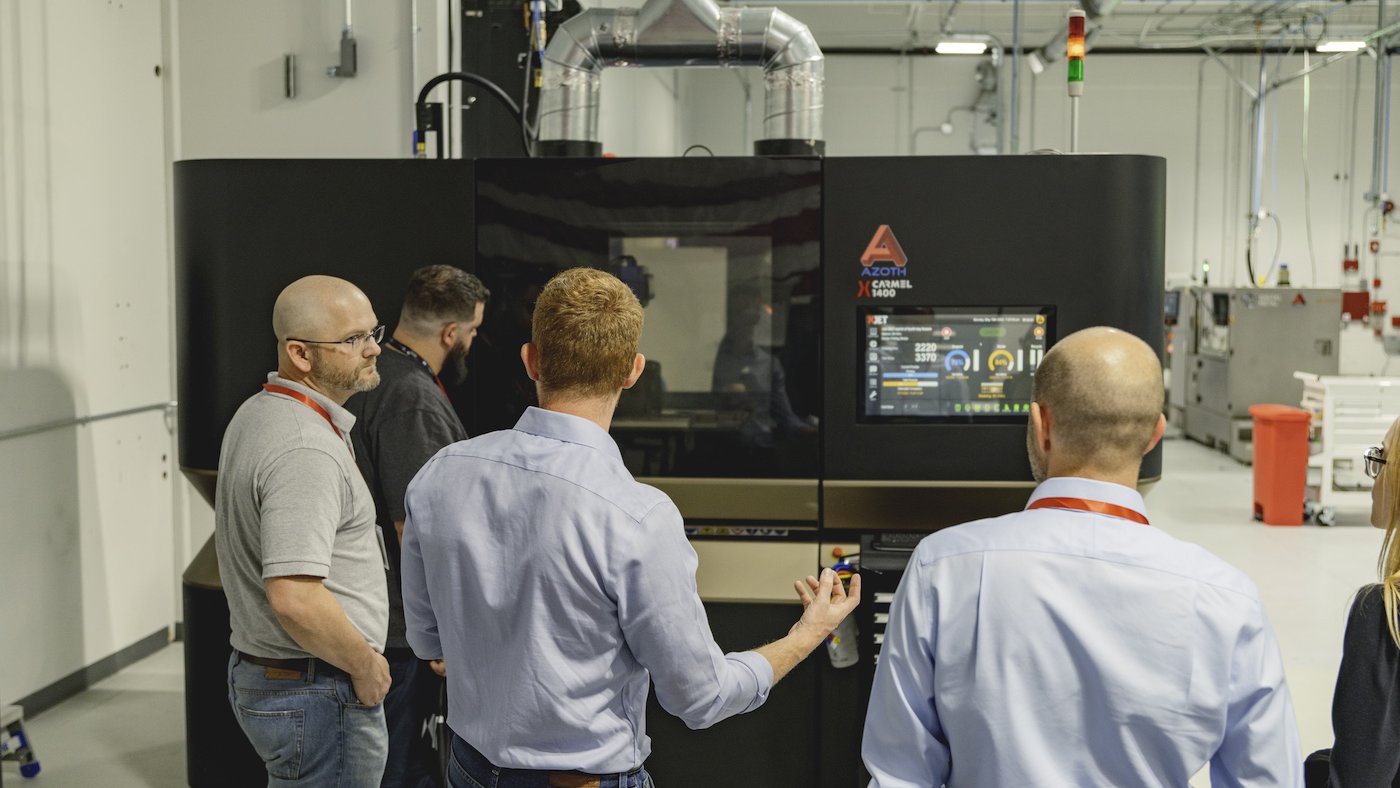
Azoth distinguishes itself as one of the select manufacturers utilizing Nano-Particle Jetting (NPJ) additive manufacturing, a technology adept at crafting exceptionally small and intricately detailed parts with an unrivaled resolution of +/- 25 microns. A transformative technology that revolutionizes the production of small surgical tools, hearing aids, dental crowns, and more, just to name a few applications.
Our expertise extends beyond printing; we handle post-processing, finishing, and rigorous inspections to deliver the highest quality end-use parts. Azoth goes beyond being a manufacturing service; we are your dedicated partner throughout the entire production journey.
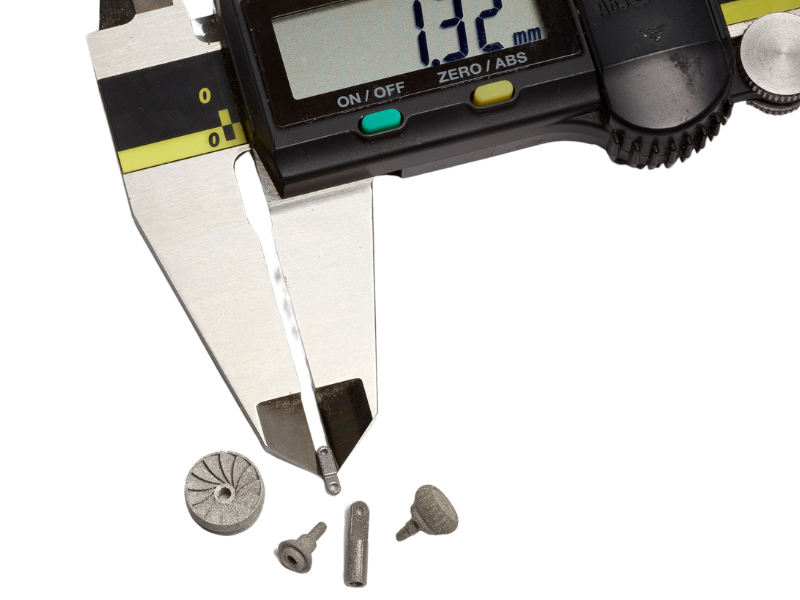
Applications in the Medical Industry
Azoth excels in the production of small surgical instrumentation and tooling. Whether handheld instruments or end effector for robotic devices, we enable the manufacturing of complex geometries with ease. Our technology allows for the customization of implants based on individual patient anatomy, ensuring the best possible fit and optimal functionality.
Whether it’s specialized equipment for medical procedures, custom fixtures, or tools for research and development, our process delivers cost-effective tailor-made solutions.
Facilitate quick iterations, allowing for the timely testing and refinement of medical device designs. Experience a more efficient prototyping phase, reducing time to market for medical solutions.
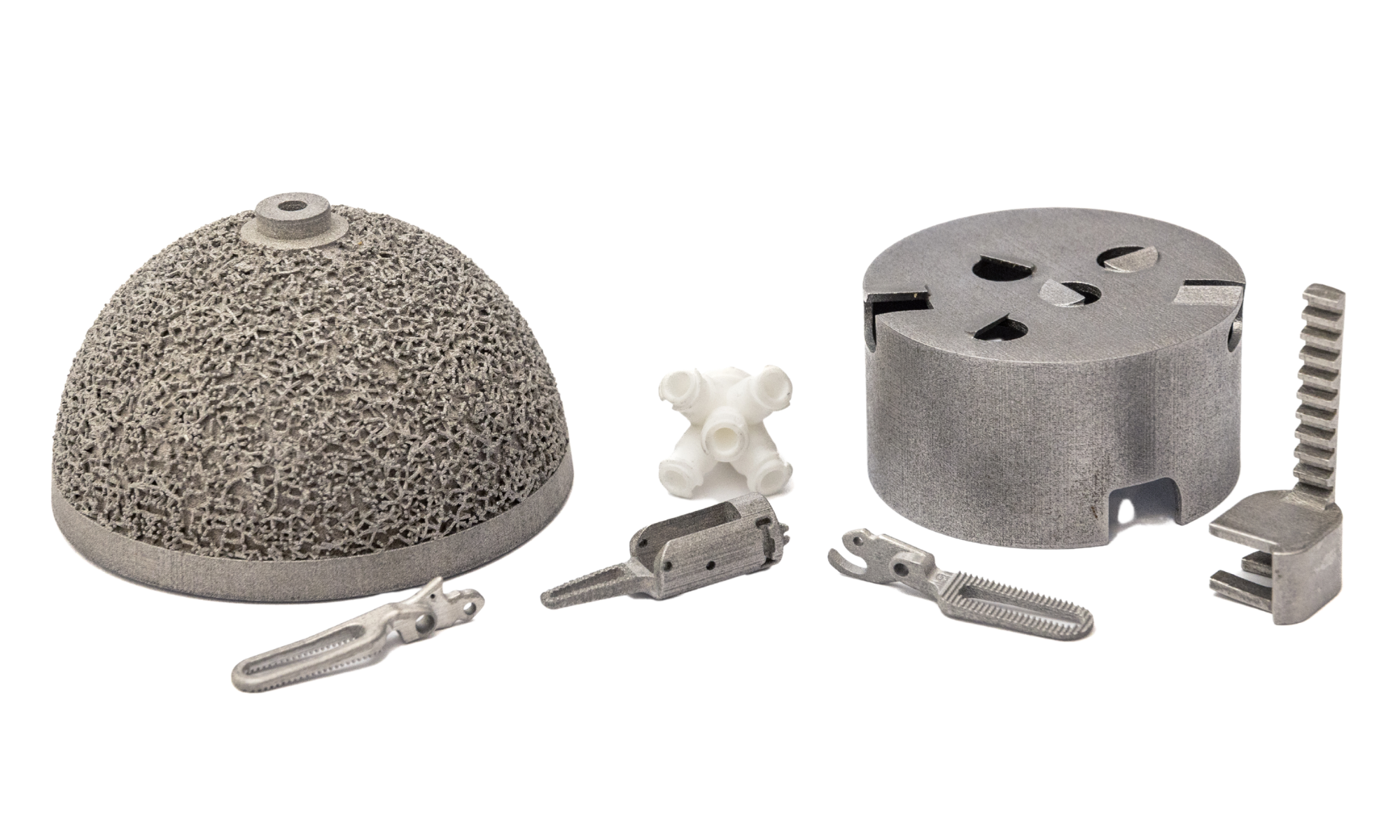
Medical Grade Quality
Azoth's commitment to quality is evident by our ISO-9001:2015 certification, signifying our dedication to maintaining stringent quality management systems, ensuring consistency, reliability, and continual improvement in our manufacturing processes.
Azoth offers a comprehensive range of materials. Every part manufactured by Azoth can be traced to its specific lot, allowing for meticulous tracking and accountability throughout the production process.
Our suite of metrology and testing equipment ensures the quality of all parts. Every manufactured component undergoes rigorous dimensional and visual evaluation. After inspection, accepted parts are accompanied by a Certificate of Inspection, verifying that every component conforms to the customers’ requirements.
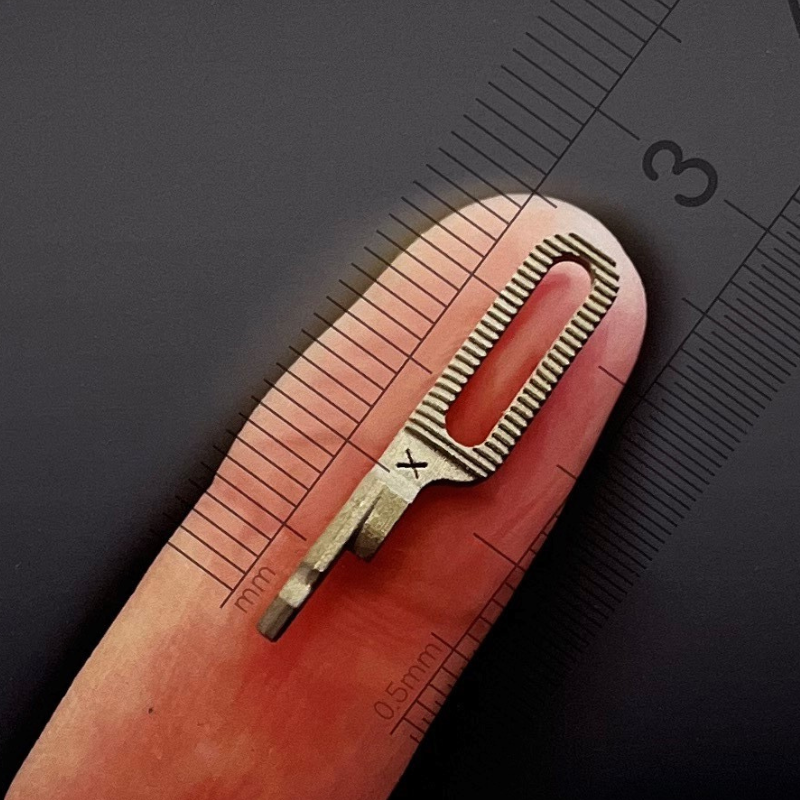