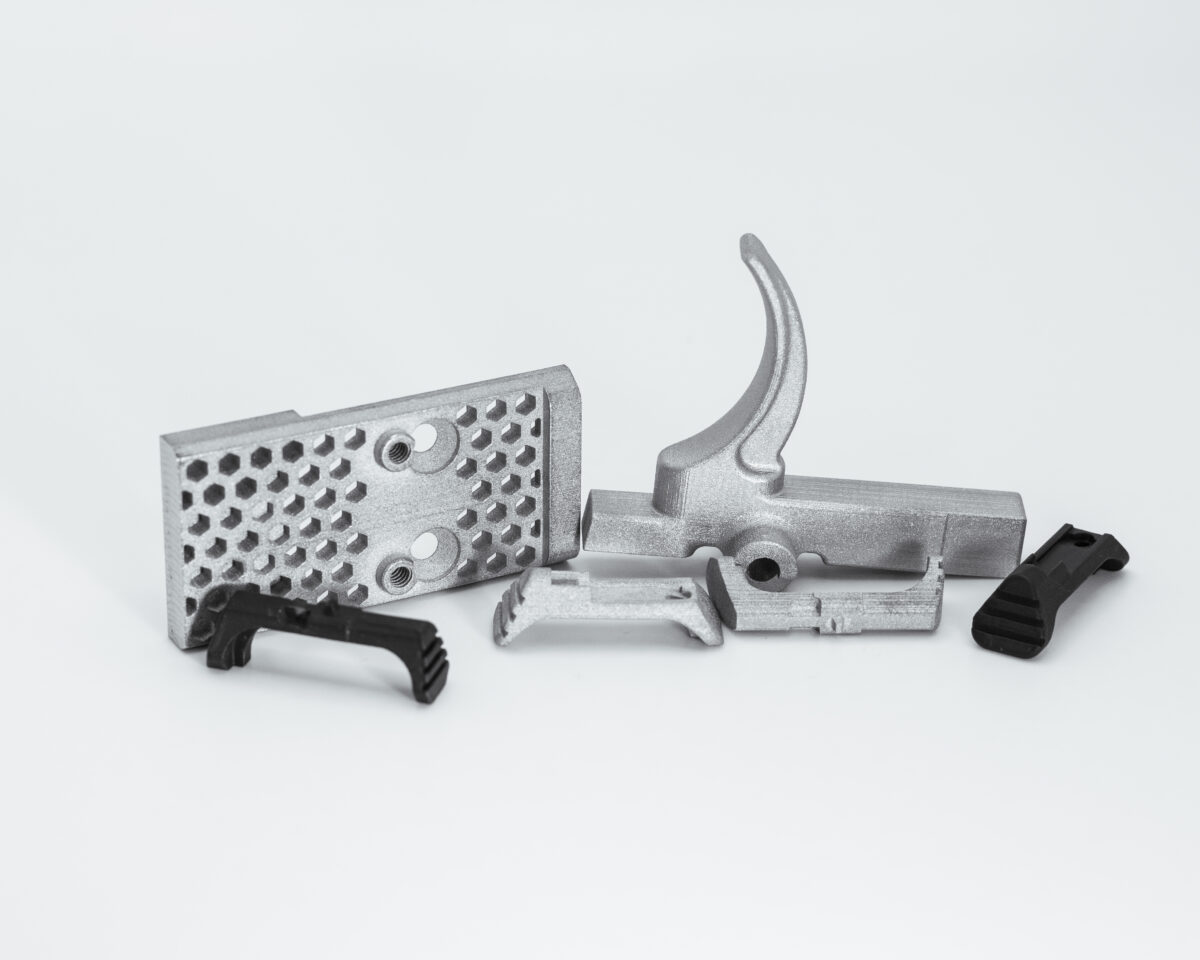
Five Reasons to Select Metal Binder Jetting with Azoth
The world of 3D printing (formally known as additive manufacturing) is a diverse landscape that encompasses a variety of technologies, materials, and equipment. To a newcomer, it can be quite overwhelming. This article will help you to navigate the terrain by guiding you through binder jet 3D printing and its top five benefits.
What is Metal Binder Jetting?
Metal binder jetting (MBJ) is a sinter-based method of 3D printing that produces highly detailed parts from powdered feedstock. Powder is evenly dispensed—whether it's metal, plastic, or even ceramic—across a build box, maintaining a precise thickness. An inkjet print head travels across the powder layer, meticulously applying a liquid binding agent, akin to glue, onto the powder layer, defining the cross section of the intended part. This sequence repeats until the part reaches its full height. Subsequently, the build box is removed, and the freshly printed components are delicately excavated, staged, and sintered. The sintering process occurs in an industrial furnace, subjecting the parts to temperatures near their melting points, thus solidifying the structure to full density.
In comparison to other metal additive manufacturing processes, MBJ is notably more cost effective. The absence of intricate and costly laser systems, coupled with faster print times, culminates in significantly reduced operating expenses. MBJ is the most scalable 3D printing technology, making it versatile for applications ranging from tailored short part runs to large-scale, high-volume production.
Despite what is advertised and seen online, the process is not as simple as “Ctrl + P.” Equipment alone does not guarantee success. Like any manufacturing process, mastery of the nuisances is what ultimately determines the quality of the part.
Azoth is the leading expert in metal binder jetting and will partner with you every step of the way. Our expertise goes beyond just printing to get you the highest quality parts at the best possible price.
But why choose metal binder jetting and why choose Azoth?
Cost
The bottom line for any part is always cost. With traditional manufacturing methods, such as CNC machining or metal injection molding, upfront investment is needed for the necessary tooling. The more intricate the part, the greater the investment.
MBJ circumvents that entirely. No matter the level of complexity, upfront investment is not needed. However, the part size and complexity can still affect the unit cost. Larger and more complex parts increase the powder and binder cost, require more handling, and limit the ability of nesting parts in prints or furnace runs.
In general, MBJ printed parts are more cost effective at low volumes, but traditional methods are more cost effective at higher volumes.
Time to Market
Accelerated time to market is an advantage often touted across various 3D printing technologies. However, MBJ takes it to the next level. Not only can you rapidly prototype through designs, but you can seamlessly transition to production on the same equipment.
With a standard 10–15-day lead time, Azoth enables designers to accelerate the prototyping phase. MBJ not only delivers authentic and functional metal prototypes but also serves as a robust validation for production. The consistency of equipment and process ensures that the same exceptional resolution and tolerance achieved in prototypes are perfectly translatable to production-level volumes. This inherent reliability positions MBJ as a game-changer for those seeking swift and dependable routes from concept to market.
Freedom of Design
MBJ doesn't just present an alternative to conventional metal powder manufacturing processes; but stands as a distinctive manufacturing method with unique advantages, capable of geometries otherwise deemed impossible. This frees designers from the constraints of traditional manufacturing, allowing lattice structures, organic forms, internal channels, and distinctive textures, to name just a few possibilities.
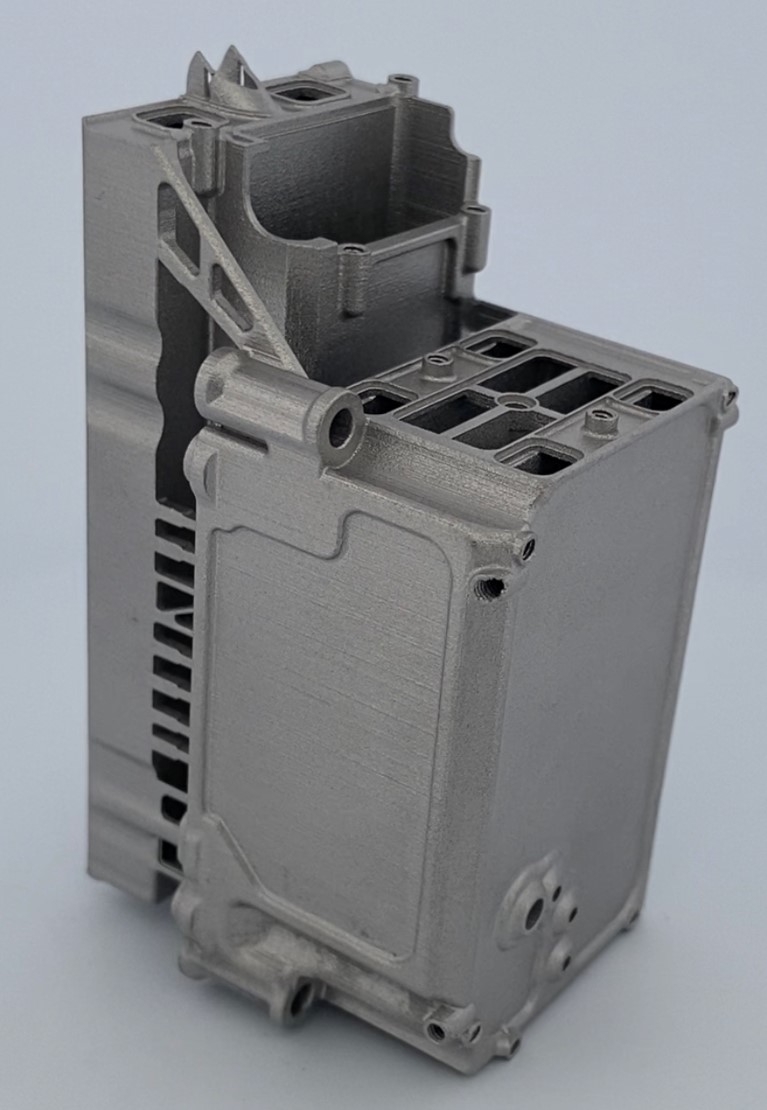

However, just because it can be printed does not promise a high-quality final part. Azoth helps with optimizing design for the MBJ processes as well as the application. We ensure your design is perfected while still capable of handling and successfully sintering.
Quality
Azoth has refined operating procedures and a strict quality control management system ensuring the utmost reliability in our manufacturing process. Drawing from real production data, we've observed a process variation following a statistically normal distribution, providing us with a clear understanding of what to anticipate. This allows us to deliver feasible solutions and set realistic expectations for our customers.
A tolerance of +/- 2% is commonplace for first run parts, with potential for +/- 1% after optimization. For components weighing less than 50 grams, a remarkable tolerance of +/- 0.75%, up to +/- 50μm, is achievable. Unlike other processes, MBJ does not experience tool wear, mold wear, or depowering of lasers, ensuring consistency across the life of production.
MBJ under the Azoth standard yields parts with isotropic mechanical properties, characterized by small grain size, absence of inclusions, and high densification. The as-printed parts show a surface roughness of 6μm RA, further refined to 3μm RA after bead blasting.
Throughput
MBJ stands out by enabling production possibilities that surpass the capabilities of other 3D printing technologies. This is evident through Azoth’s ongoing and growing production for the automotive industry. MBJ's distinct ability to nest components within a single build is a game-changer, facilitating the simultaneous manufacturing of a highly diverse product mix.
Throughput is dependent upon part size and complexity. Estimated production volumes compared to part size are seen below.
- 1,000s of parts per year for parts 50mm in largest dimension
- 10,000s of parts per year for parts 30mm in largest dimension
- 100,000s of for parts below 10mm in largest dimension
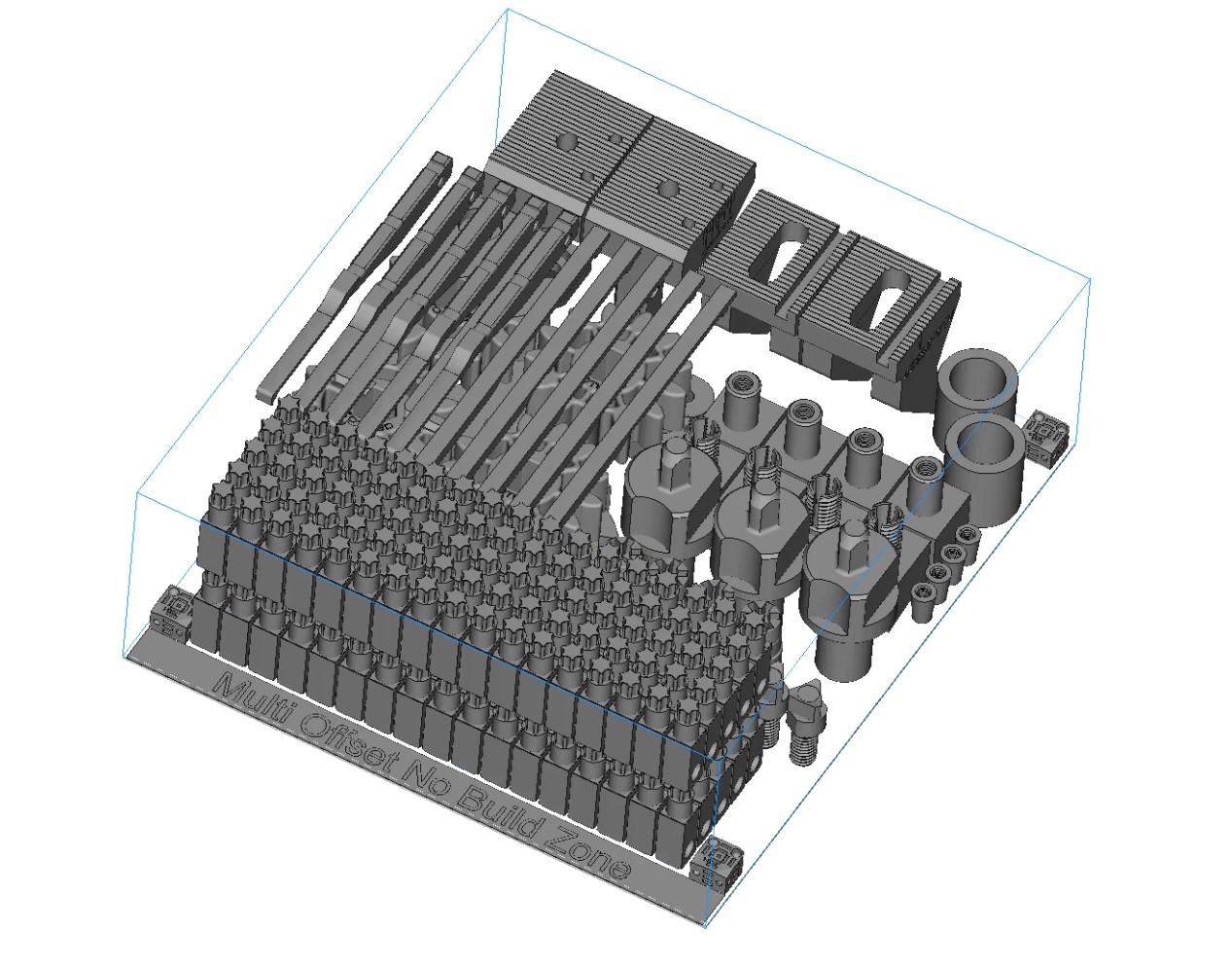
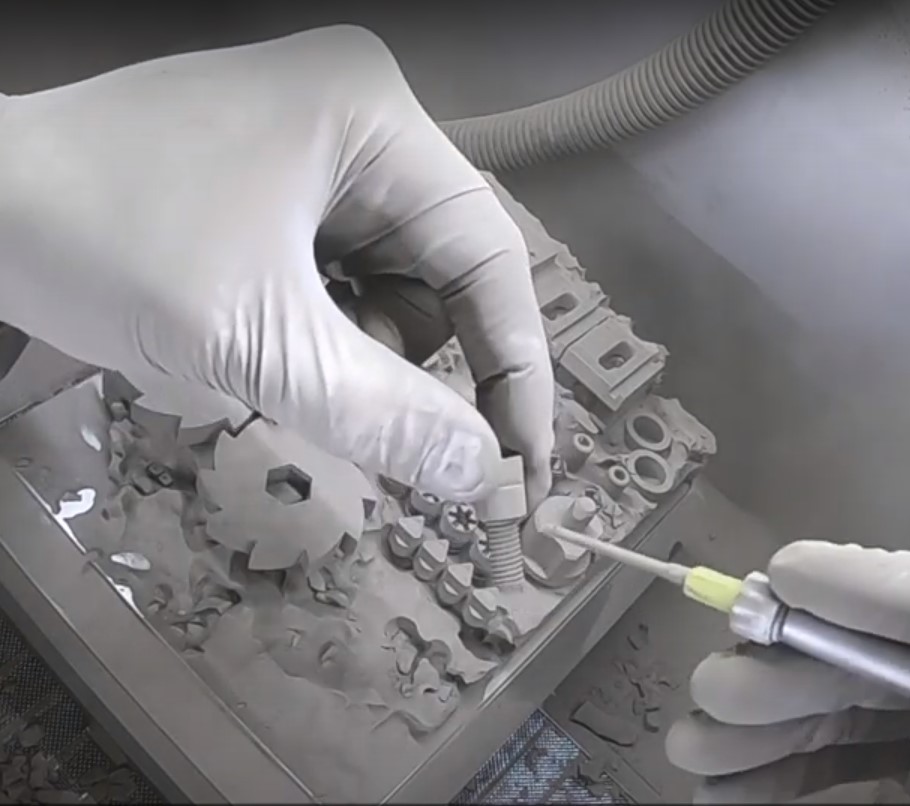
Peeling Back the Layers
In the ever-growing landscape of 3D printing, Binder Jetting Technology is a production capable process that stands out from the rest. With a competitive cost model, unrivaled speed, unique design capabilities, consistent quality, and superior throughput, MBJ is ideal for a variety of applications.
However, considerations for the process must be included in the design phase. Azoth is ready to partner with you to demystify the complexities of MBJ and showcase its potential.
When ready, submit your parts to Azoth for review. Still have questions? Reach out to our application engineering team at info@azoth3D.com with any questions.