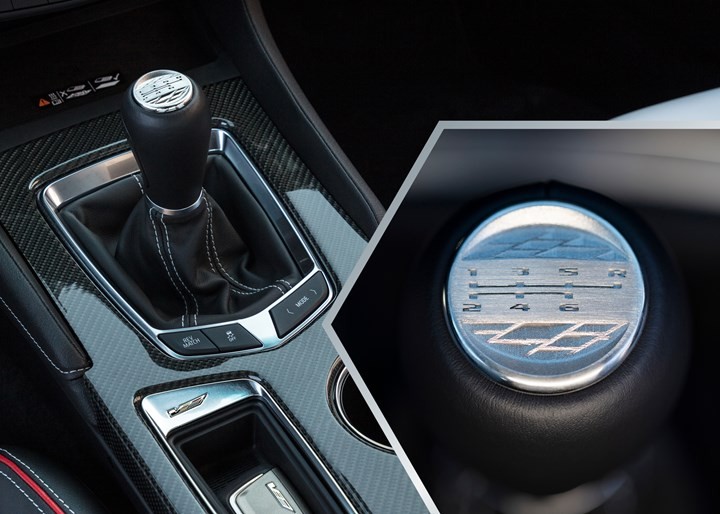
Azoth Produces First Metal 3D Printed Part Via Binder Jetting On A Production Vehicle For General Motors
In News & Updates by AZOTH3D
Azoth, a vertically integrated additive manufacturing company, is manufacturing the first metal 3D printed part using binder jetting on a General Motors production vehicle.
A unique, 3D printed medallion produced by Azoth sits on the manual shifter knob of the new 2022 Cadillac Blackwing V-series models, which features a manual transmission as well as additional 3D parts developed by General Motors.
Azoth is a leader in the metal binder jetting space and through its advanced 3D printing processes, it can save time and costs when producing parts while passing all Production Part Approval Process (PPAP) requirements, said Azoth General Manager and Co-Founder Cody Cochran.
“Binder jetting enables quantities at the speeds and quality levels demanded by automotive production,” Cochran said. “We use a disruptive process that is more efficient than other technologies. We can print the prototype of a part every five or six days, while other processes and technology can take three to six months building molds, retooling and going through multiple suppliers.”
“It is exciting to work with a forward-thinking company like GM who understands the benefits that additive manufacturing brings to production. I believe this is a breakthrough application for the 3D printing industry and a major win for metal binder jetting, proving this is a production ready process,” he said.
The new Cadillac CT4-V Blackwing as well as the CT5-V Blackwing features the manual transmission, a popular feature for driving enthusiasts.
In a press release issued late last year, Cadillac said that by leveraging additive manufacturing, it was able to reduce costs and waste when developing the manual transmission.
Azoth, a vertically integrated additive manufacturing company, is manufacturing the first metal 3D printed part using binder jetting on a General Motors production vehicle.
A unique, 3D printed medallion produced by Azoth sits on the manual shifter knob of the new 2022 Cadillac Blackwing V-series models, which features a manual transmission as well as additional 3D parts developed by General Motors.
Azoth is a leader in the metal binder jetting space and through its advanced 3D printing processes, it can save time and costs when producing parts while passing all Production Part Approval Process (PPAP) requirements, said Azoth General Manager and Co-Founder Cody Cochran.
“Binder jetting enables quantities at the speeds and quality levels demanded by automotive production,” Cochran said. “We use a disruptive process that is more efficient than other technologies. We can print the prototype of a part every five or six days, while other processes and technology can take three to six months building molds, retooling and going through multiple suppliers.”
“It is exciting to work with a forward-thinking company like GM who understands the benefits that additive manufacturing brings to production. I believe this is a breakthrough application for the 3D printing industry and a major win for metal binder jetting, proving this is a production ready process,” he said.
The new Cadillac CT4-V Blackwing as well as the CT5-V Blackwing features the manual transmission, a popular feature for driving enthusiasts.
In a press release issued late last year, Cadillac said that by leveraging additive manufacturing, it was able to reduce costs and waste when developing the manual transmission.
Azoth, a vertically integrated additive manufacturing company, is manufacturing the first metal 3D printed part using binder jetting on a General Motors production vehicle.
A unique, 3D printed medallion produced by Azoth sits on the manual shifter knob of the new 2022 Cadillac Blackwing V-series models, which features a manual transmission as well as additional 3D parts developed by General Motors.
Azoth is a leader in the metal binder jetting space and through its advanced 3D printing processes, it can save time and costs when producing parts while passing all Production Part Approval Process (PPAP) requirements, said Azoth General Manager and Co-Founder Cody Cochran.
“Binder jetting enables quantities at the speeds and quality levels demanded by automotive production,” Cochran said. “We use a disruptive process that is more efficient than other technologies. We can print the prototype of a part every five or six days, while other processes and technology can take three to six months building molds, retooling and going through multiple suppliers.”
“It is exciting to work with a forward-thinking company like GM who understands the benefits that additive manufacturing brings to production. I believe this is a breakthrough application for the 3D printing industry and a major win for metal binder jetting, proving this is a production ready process,” he said.
The new Cadillac CT4-V Blackwing as well as the CT5-V Blackwing features the manual transmission, a popular feature for driving enthusiasts.
In a press release issued late last year, Cadillac said that by leveraging additive manufacturing, it was able to reduce costs and waste when developing the manual transmission.
Azoth, a vertically integrated additive manufacturing company, is manufacturing the first metal 3D printed part using binder jetting on a General Motors production vehicle.
A unique, 3D printed medallion produced by Azoth sits on the manual shifter knob of the new 2022 Cadillac Blackwing V-series models, which features a manual transmission as well as additional 3D parts developed by General Motors.
Azoth is a leader in the metal binder jetting space and through its advanced 3D printing processes, it can save time and costs when producing parts while passing all Production Part Approval Process (PPAP) requirements, said Azoth General Manager and Co-Founder Cody Cochran.
“Binder jetting enables quantities at the speeds and quality levels demanded by automotive production,” Cochran said. “We use a disruptive process that is more efficient than other technologies. We can print the prototype of a part every five or six days, while other processes and technology can take three to six months building molds, retooling and going through multiple suppliers.”
“It is exciting to work with a forward-thinking company like GM who understands the benefits that additive manufacturing brings to production. I believe this is a breakthrough application for the 3D printing industry and a major win for metal binder jetting, proving this is a production ready process,” he said.
The new Cadillac CT4-V Blackwing as well as the CT5-V Blackwing features the manual transmission, a popular feature for driving enthusiasts.
In a press release issued late last year, Cadillac said that by leveraging additive manufacturing, it was able to reduce costs and waste when developing the manual transmission.